APECS | Über den Beitrag des Fraunhofer IMS zur Pilotlinie
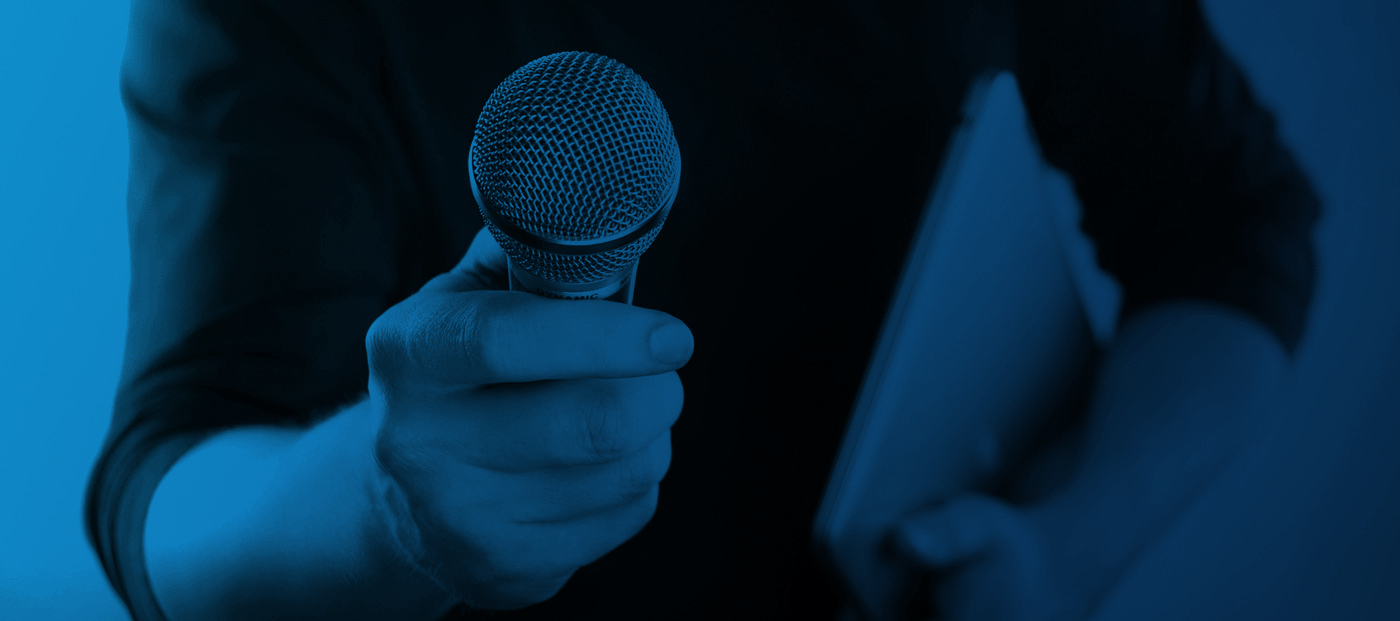
Die APECS-Pilotlinie (kurz für »Advanced Packaging and Heterogeneous Integration for Electronic Components and Systems«) bündelt das Know-how von 10 Partnern aus 8 europäischen Ländern, um in den kommenden Jahren eine umfassende europäische Forschungsinfrastruktur im Bereich Heterointegration und Advanced Packaging aufzubauen. Auch das Fraunhofer IMS ist als in der FMD kooperierendes Institut am Aufbau der Pilotlinie beteiligt. Wir haben mit Dr. Sascha Weyers, Abteilungsleiter Technology, darüber gesprochen, welche Expertise das Fraunhofer IMS in APECS einbringt und wie er persönlich auf die Entwicklung der Pilotlinie blickt.
Herr Dr. Weyers, Sie arbeiten seit 2001 am Fraunhofer IMS. In welchen Bereichen sind Sie dort tätig?
Begonnen habe ich am Institut im Bereich Drucksensoren und Fertigungssteuerung, bevor ich mich dem Thema CMOS- und MEMS-Entwicklung gewidmet habe. Seit 2020 bin ich verantwortlich für die Gesamttechnologieentwicklung am Institut und im November 2024 habe ich außerdem die Leitung für APECS am Fraunhofer IMS übernommen.
APECS ist der Name der europäischen Pilotlinie, die im November 2024 gestartet ist. Sie wird von der Fraunhofer-Gesellschaft koordiniert und von der FMD implementiert. Ziel ist die Stärkung der technologischen Resilienz Europas und der europäischen Halbleiterindustrie. Welche Expertise bringt das Fraunhofer IMS in die Pilotlinie ein?
Unsere Expertise, die wir in die Pilotlinie einbringen, lässt sich grob in drei Bereiche gliedern: Das ist zum einen das Thema Integration und Kombination in der Photonik und zum anderen in der Infrarot-Sensorik. Außerdem verfügen wir über viel Know-how in der Charakterisierung. In der integrierten Photonik sind wir hier am Institut schon sehr weit – allerdings möchten wir unsere Expertise dahingehend ausbauen, dass wir Schnittstellen nach außen schaffen. Das heißt, die Kombination von unseren Technologien mit externen Technologien ist etwas, was wir im Rahmen von APECS verstärken werden. Außerdem wollen wir daran arbeiten, dass beispielsweise Bauelemente im Bereich Backend-Optik so gestaltet werden, dass sie noch besser mit anderen Technologien kombinierbar sind.
Ein weiterer etablierter Bereich ist bei uns die Weiterentwicklung der Infrarot-Sensorik, in der wir erforschen, wie Sensorik und Elektronik effektiv kombiniert werden können. Ein wesentlicher Aspekt dabei ist die Entwicklung entsprechender Design-Tools, also das Schaffen von Schnittstellen, um einen durchgängigen Entwicklungsfluss sicherzustellen. Ziel ist es, unseren Kunden ein umfassendes Gesamtpaket statt einzelner Komponenten anbieten zu können. Und natürlich geht es auch um die Kommunikation der Chips mit der Außenwelt, wenn diese in Geräte und Anlagen eingebaut und ihre Informationen weiterverarbeitet werden.
Der dritte Kernbereich unserer Expertise ist die Charakterisierung, bei der wir z. B. einzelne Materialien oder Schichten untersuchen. Dabei geht es nicht nur darum, zu testen, ob ein Produkt funktioniert oder nicht, sondern auch um die Identifikation von Abhängigkeiten, Verläufen und Optimierungspotenzialen. Das ist insbesondere im Hinblick auf neue Technologien und bei der Kombination von Komponenten sehr relevant.
Zusammengefasst bedeutet das: Im Rahmen von APECS fokussieren wir uns am Fraunhofer IMS darauf, Prozesse und Werkzeuge zu entwickeln, die die Integration verschiedener Komponenten vereinfachen. Dazu zählen Process- und Assembly-Design-Kits (P/ADKs) sowie Design-Flows, die für die hochentwickelte 2.5D- und 3D-Integration sowie die quasi-monolithische Integration (QMI) benötigt werden. Am Ende ist es ein Teilziel der APECS-Pilotlinie, keine Einzelkomponenten anzubieten, sondern einen gesamten Design-Flow. So soll sichergestellt werden, dass die verschiedenen Technologien, die im Rahmen von APECS entwickelt werden, miteinander kombiniert werden können.
Lassen Sie uns auf diese Technologien im Detail schauen und mit der 2.5D- und 3D-Integration beginnen. Was steck hinter diesem Ansatz?
Mit beiden Prozessen wird versucht, zwei oder mehr Chips möglichst platzsparend und effizient miteinander zu verbinden. Bei der 2.5D-Integration werden hierzu die Chips auf einem Interposer nebeneinander platziert, was eine hohe Dichte und schnelle Kommunikation zwischen ihnen ermöglicht. Eine noch höhere Integration und Leistungsdichte lässt sich mit der 3D-Integration erreichen. Hierbei werden Chips übereinandergestapelt, sodass vertikale Verbindungen zwischen ihnen entstehen. Das heißt, am Ende entsteht bei diesen Integrationsmethoden zwar ein System, die einzelnen Bereiche sind aber noch zu erkennen. Die QMI geht noch einen Schritt weiter.
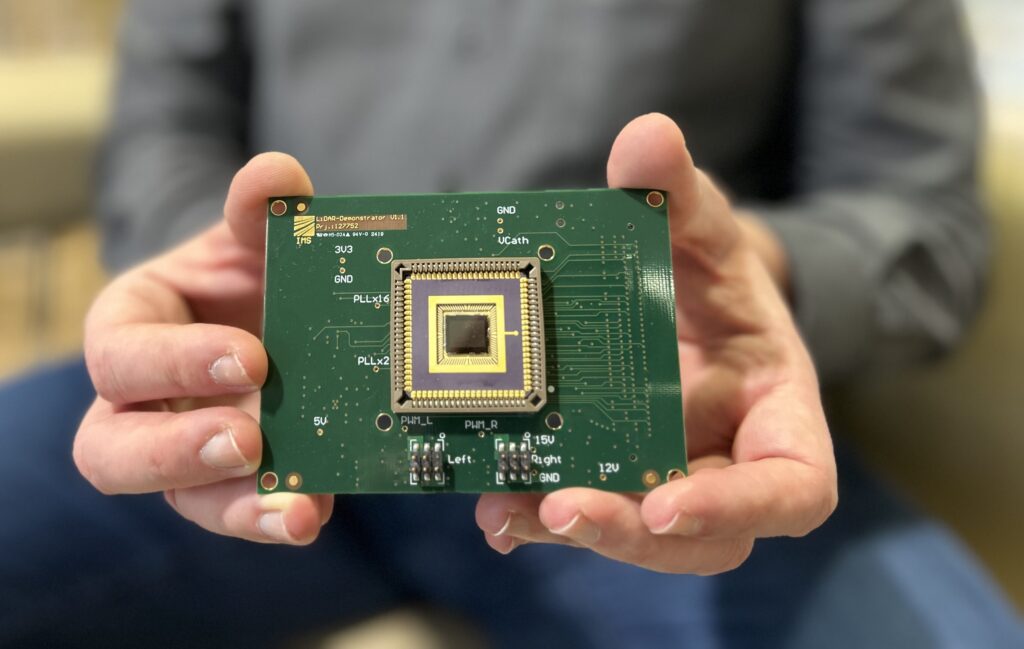
Was bedeutet einen Schritt weitergehen in diesem Fall?
»Bei der QMI sollen Chips sozusagen in Chips integriert und direkt aufeinander aufgebracht werden. Das funktioniert, indem beispielsweise Bereiche in einem Chip freigelegt werden und ein zweiter Chip anschließend darin integriert wird. Man kann dann damit weiterarbeiten als handele es sich um einen einzigen Chip. Das bedeutet, dass z. B. die Metallisierung für beide gemeinsam erfolgen kann. Die Integration wird also bereits in den Prozess eingebaut. Das hat auch zur Folge, dass Methoden, die sonst eigentlich bei der Chipherstellung genutzt werden, dementsprechend auch in der Kombination zum Einsatz kommen können. Das ist der große Unterschied zu den anderen Integrationsmethoden.«
Wie genau profitieren Sie am Fraunhofer IMS von der QMI?
Die QMI ist sehr wichtig für optische Sensoren, um eine enge Verbindung zwischen dem optischen Teil und der Elektronik herzustellen. Denn lange Verbindungen sind in diesem Zusammenhang ungünstig und die QMI ermöglicht es, die Vorteile durch die hohe Integrationsdichte nutzen zu können. Wie beschrieben, beschäftigen wir uns am Fraunhofer IMS viel mit der Integration und Kombination verschiedener Komponenten, z. B. Elektronik und Sensorik, und an dieser Stelle hilft uns die QMI, Schnittstellen zu schaffen und Fertigungsprozesse zu vereinfachen.
Auf das Stichwort Schnittstellen möchten wir gerne noch konkreter eingehen, denn im Rahmen von APECS sollen am Fraunhofer IMS außerdem Complex-IPs für optische Komponenten (Phasenschieber) und Schnittstellen-Technologien, die hohe Datenraten unterstützen, entwickelt werden. Können Sie das erklären?
Eine komplexe IP im Kontext von optischen Komponenten ist die Kombination eines optischen Teils mit einem elektronischen Teil. Grundsätzlich gilt: Im optischen Teil gibt es Wellenleiter und Bauelemente, die das Licht beeinflussen. Diese Bauelemente sollen gesteuert werden, was in der Regel elektronisch von außen erfolgt. Im einfachsten Fall bedeutet das, der Wellenleiter wird erwärmt, die Eigenschaften ändern sich und auf diese Weise kann das Licht gesteuert werden. Ziel dieser Complex-IPs ist es nun, diesen Prozess als fertiges System anzubieten und nur noch ein Bauteil zu gebrauchen. Wir versuchen in unserer Forschung daher, bestimmte Komponenten vorab zu definieren, um Kunden Entwicklungsarbeit abzunehmen und ihnen fertige, genau definierte Komponenten anzubieten.
Wie kann eine solche Schnittstelle in das Design integriert werden?
Das kann man sich wie einen Lego-Baukasten vorstellen. Design bedeutet erstmal, dass es verschiedene vorab definierte Bauteile gibt. Je nachdem, was ich brauche für meine Forschung, kann ich dann bestimmte Bauteile auswählen und sie miteinander verbinden. Anwender:innen haben so die Möglichkeit, sich wie aus einem Katalog die Bauteile herauszusuchen, die sie benötigen, und diese miteinander zu verbinden. Das erfolgt meist automatisch. Die Design-Software soll dazu führen, dass die Komponenten möglichst effizient platziert werden können. Wir möchten den Kunden ein fertiges Bauteil anbieten inklusive einer detaillierten Beschreibung. Es soll klar sein, wie das Bauteil eingebaut werden muss, wie es sich verhält und natürlich, was es leistet. Das bedeutet, wir müssen die Bauteile, bevor wir sie an Kunden geben, charakterisieren. Es werden beispielsweise Signale ausgesendet, um zu testen, wie sich das Bauteil verhält und Modelle zu erstellen. Diese so generierten Modelle können Kunden dann für ihre Simulationen nutzen.
Sie haben das Thema Charakterisierung schon angesprochen. Für APECS ist in Hinblick auf die Entwicklung von Demonstratoren zudem das Thema Validierung sehr wichtig. Würden Sie dazu ein bisschen mehr erzählen?
Es gibt zwei Aspekte der Validierung. Das eine ist der technologische Bereich. Hier wird überprüft, ob sich eine entwickelte Technologie so verhält, wie es zu erwarten ist. Grundlage ist die schon angesprochene Charakterisierung der Bauteile, die wir im Rahmen von APECS durchführen. Der andere Aspekt der Validierung bezieht sich auf das Gesamtprojekt, denn wir müssen und wollen natürlich sicherstellen, dass unsere Pilotlinie insgesamt funktioniert. Also: Sind reibungslose Abläufe garantiert? Sind die einzelnen Komponenten einsatzfähig? An dieser Stelle werden die Demonstratoren, die im Rahmen von APECS entwickelt werden, relevant. Mithilfe dieser Demonstratoren können wir zeigen, dass beispielsweise die Kombination verschiedener Bauteile in der Praxis erfolgreich möglich ist, sowohl hinsichtlich des Ablaufs als auch im Hinblick auf die Funktionen. Auf diese Weise stellen wir sicher, dass sich unsere Arbeit in die richtige Richtung entwickelt und wir am Ende den Kunden fehlerfreie Produkte anbieten können.
In APECS arbeitet ein europäisches Konsortium mit 10 Partnern aus 8 europäischen Ländern zusammen. Das Fraunhofer IMS arbeitet eng mit dem VTT aus Finnland zusammen, insbesondere bei Verbindungstechnologien (Interconnect). Was bedeutet Interconnect?
»Interconnect bedeutet, dass neben der mechanischen auch eine elektrische Verbindung zwischen den Chips hergestellt wird. Bei Chips, die man direkt aufeinanderstapelt, ist die einfachste Möglichkeit, dies zu realisieren, Löcher zwischen den Chips zu generieren und ein leitendes Material einzufüllen. Wichtig ist, zu verhindern, dass Schichten, die vorher aufgebracht wurden, durch diesen Schritt zerstört werden. Eine Alternative zu diesem Vorgehen besteht darin, an der Oberfläche beider Chips elektrische Verbindungen vorzubereiten, die sich gegenüberliegen. Auf diese Weise entsteht beim Aufeinanderstapeln automatisch eine elektrische Verbindung. Beide Verfahren haben Vor- und Nachteile.«
Wie sieht die Zusammenarbeit mit dem VTT aus?
»Gemeinsam mit dem VTT suchen wir nach Materialkombinationen oder Prozessabläufen, die die besten Eigenschaften für diese Verbindungen liefern, beispielsweise einen geringen Widerstand und hohe Zuverlässigkeit. Die Forschenden am VTT sind besonders stark in der Aufgabe, solche Verbindungen zu realisieren, und in den Bereichen Materialentwicklung und Abscheidemethoden. Wir ergänzen uns in unseren Kompetenzen sehr gut. Hierbei arbeiten wir im Rahmen von APECS auch eng mit dem Fraunhofer ENAS zusammen und können Synergien nutzen.«
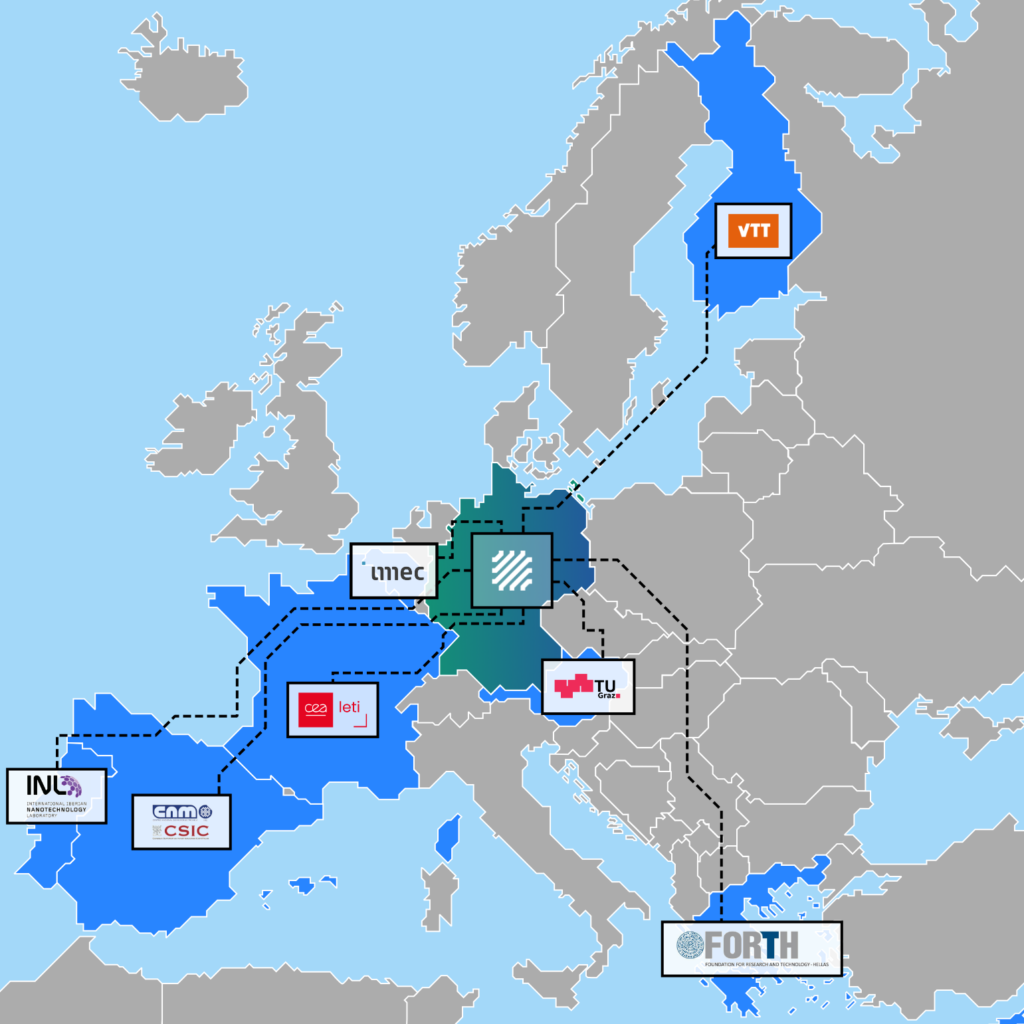
Was ist aus Ihrer Perspektive die größte Stärke von APECS?
Die größte Stärke ist die europäische Zusammenarbeit und die dezentrale Forschungsstruktur, die aufgebaut wird. Hier profitieren wir auf jeden Fall davon, dass wir durch die FMD in Deutschland schon eine sehr gute Vorarbeit hinsichtlich der Zusammenarbeit im Bereich Mikro- und Nanoelektronik haben. Es gibt ein breites Spektrum von Instituten, die alle über spezifische Expertise verfügen und Erfahrung mit Kooperationen, beispielsweise in der Koordination von Kundenanfragen, mitbringen. Mit der APECS-Pilotlinie bringen wir diese Zusammenarbeit auf ein neues Level. Wir wollen die Voraussetzungen dafür schaffen, verschiedene Technologien miteinander zu verbinden und in die industrielle Anwendung zu bringen. Durch das Entwickeln gemeinsamer Tools werden wir Kunden viel schneller Lösungen aus einem breiten Portfolio anbieten können.
Haben Sie dafür ein konkretes Beispiel?
Heute ist die Kombination verschiedener Technologien ein Schlüsselaspekt für die Industrie. Während früher einzelne Funktionen in Herstellungsprozessen miteinander kombiniert werden konnten, erfordert die Integration zusätzlicher Funktionen mittlerweile einen hohen Aufwand in der Vorarbeit und Umsetzung, damit eine nahtlose Funktionalität gewährleistet ist. Nehmen wir das Beispiel Erfassung und Verarbeitung unterschiedlicher Sensordaten, beispielsweise Licht und Druck. Anstelle einer Entwicklung, die beides gleichzeitig ermöglicht, kann, indem jeweils Basis-Chips mit Druck- und optischen Sensoren kombiniert werden, eine robuste Lösung entstehen, die den hohen industriellen Anforderungen gerecht wird. Das reduziert die Notwendigkeit, bei jeder Anpassung von vorn beginnen zu müssen und ermöglicht durch jeweils spezialisierte Chips eine effizientere Verarbeitung von Daten innerhalb des Sensors. Die Arbeit in unserer Pilotlinie leistet dazu einen wichtigen Beitrag.
Auf welche Aufgaben im Projekt freuen Sie sich am meisten?
Ich freue mich am meisten auf die Zusammenarbeit zwischen den verschiedenen Technologiebereichen und auf deren technische Umsetzung, beispielsweise mithilfe der angesprochenen Design-Tools. Dazu braucht es Austausch über Abteilungs- und Institutsgrenzen hinweg. Das finde ich sehr spannend, denn so lerne auch ich in meiner Arbeit noch dazu.